RPO Mini-Standard (4' high x 12' wide x 30' long) The RPO Mini-Standard is a great all-around mini-ramp. The diminsions make it perfectly suitable for the backyard or elsewhere. The 4' height and 12' width make this ramp a great build for beginning and expert riders alike. The guardrails shown in the drawings are recommended, but optional!
Last year we built a backyard mini ramp for our son’s 8th birthday. He was stoked on it and we even played hooky from school for a day so he could help us build it. The process of building a mini ramp is really straightforward, but here are the steps you need to take to ensure you build a mini ramp that will last you for years to come.
- Put a screw into the 2x4 that is 6' 10' away from your starting point. 6' 10' is the transition radius, If you want your ramp to be steeper, decrease this length (a transition radius of under 3.5 feet would result in your ramp having vert). You can use the ramp tool to preview the plywood cut if you make adjustments.
- Free Mini Ramp Plans. A skateboard mini ramp is basically a shorter version of the half pipe ramp. It does not move toward vertical in its slope and has extensions on both the sides for standing. It has a flat base and is shorter in length than a half pipe.
Find a good set of mini ramp plans
Building a backyard mini ramp starts with a great set of plans. There are a few great resources out there, but best we’ve found is from DIY Skate Ramps. They have a bunch of great plans for ramps, rails, and how to set up almost everything. We referred to this site often when building our ramp.
You can use the plans from the site and build your mini ramp exactly to their specs or modify it to meet your needs.
Buy a mini ramp kit
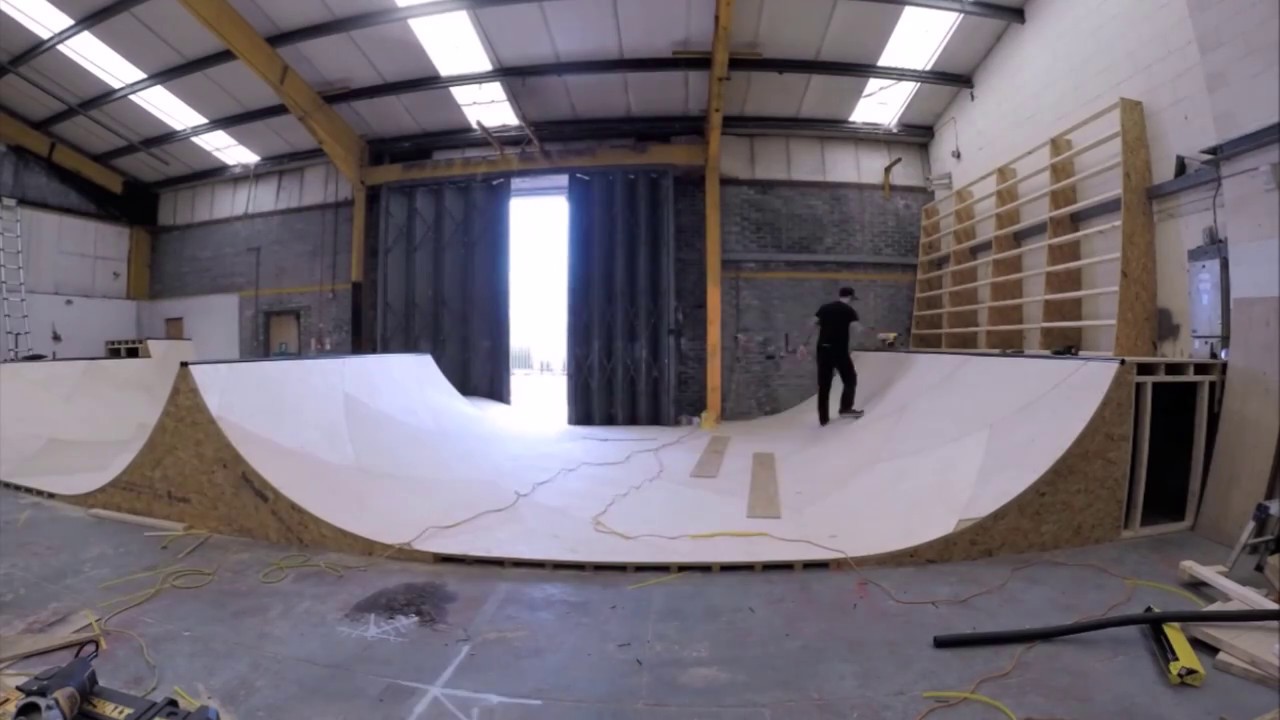
Buy or build a mini ramp is always a big question. If you want to skip the process of figuring out the plans and cutting the lumber yourself, you can order a mini ramp kit. These kits come pre-cut and include instructions for assembly. You’ll need a few tools like a cordless drill to build the ramp yourself, but buying a kit saves a lot of time in designing plans and saves money in building it yourself.
Buying a mini ramp kit is a great middle ground for DIYers and families who want to lean on the experience of ramp builders, but also want the satisfaction of building the ramp themselves.
We ordered a 3.5 x 12 mini ramp from Keen Ramps which is based in Long Beach, CA, but they ship everywhere. The founder, Cory Keen, has been a fixture on the local skate scene for years and as a skater, he knows exactly how a ramp should be built and what features skaters value the most in a ramp.
It took us 2-days to build our ramp, and we took the time to paint the plywood layers for added moisture protection. We ordered our ramp with painted sides, back, and deck which adds to the longevity of the ramp.
Clear and level the ground below your mini ramp
It’s important to start your mini ramp build right by making sure the ground you are building on is solid. Ideally you want to build your ramp on a level concrete slab, but many times that’s not available in a backyard.
Our mini ramp is built on the back part of our yard which slopes down to assist with water runoff. The slope is ideal to prevent water from pooling but not great for building a skate ramp.
Our mini ramp is 12 feet wide x 24 feet long x 3 1/2 feet tall with a 7 foot transition. This is an average sized mini ramp that takes up a good portion of our yard space.
We built the ramp over a dilapidated lawn area that was filled with weeds and a few rocks. We made sure to clear the area of as much debris and rocks as we could before we laid out our pavers that would serves as the foundation for our ramp.
With the pavers placed on each corner, down the middle, and along the sides, we had plenty of support for our ramp. We made sure tamp down the ground where each paver would sit as we didn’t want any shifting of the foundation.
To build the foundation we started in a high corner and started laying out the 2x4s. We checked the level of each additional foundation 2×4 as we built away from the corner. If an area was too low, we would add another paver to even out the height.
When we were finished the high point had two pavers and the low point was brought up by 4 pavers to match it.
Tools you need to build a mini ramp
If you don’t buy a kit, you’ll need to cut every piece of lumber yourself. The proper tools which make this much easier. We recommend the following tools for building a mini ramp.
- Miter saw
- Circular saw
Cordless drill/driver - Countersink bit
- Tape measure
- Level
- Carpenters pencil
- Star or Philips bit
- Safety glasses
Buying wood for your ramp
Your best bet for finding the wood you need to assemble your ramp is by visiting Home Depot or Lowe’s. Each of these stores can cut the lumber to the desired size you need which will save you time at home, and also make the wood easier to transport.
You may also save a bit more money by visiting a local lumber yard. Check-in with a salesperson there, as lumber is sold by yard foot, which is a different measurement compared to what you’ll find at a home center.
Protect your ramp from rain and moisture
The best way to ensure your ramp lasts for years is to paint it. It will take a bit longer to paint and wait for it to dry before you can start skating, but it’s well worth it. We ordered our Keen Ramp with the painted option which means they painted the transition sides, back, and deck.
We took the time to paint the bottom layer of plywood which adds an extra layer of protection. We don’t get much rain here in LA, but we get plenty of moisture in the evenings that often times the skate surface is completely wet in the morning.
The next important step to protect your ramp from moisture is to invest in a premium skate surface. A premium skate surface will be water and weather resistant, and also provide a more consistent and smooth skating surface for the life of the product.
1/4″ painted plywood will work, but it won’t last long, and forget about using masonite as it will start falling apart as soon as it gets wet.
Keen Ramps offers Skatelite as option, but it’s very expensive. From $150-$200 per 4×8 sheet. Our ramp needed 8 sheets, so do the math. We still wanted a premium skate surface without the high cost, and came across Gatorskins after skating a friends ramp in Encinitas.
Gatorskins offer a similar look and feel as Skatelite, but at more reasonable cost at $129 per 4×8 sheet, which offers quite a significant savings. We decided to go with Gatorskins and couldn’t be more stoked on the performance of this surface. They offer a few different colors, so give them a call to find what you like.
We also used stainless steel hex head screws to install the Gatorskins surface, as stainless steel won’t “bleed” and mark up your ramp and hex heads provide great grip, holding, and driving strength into the plywood and lumber material compared to a philips head.
Start Skating
Once you’ve installed the last sheet of plywood or Gatorskins, it’s time to skate.
Make sure you inspect your ramp regularly for screws that might be loose or coming up. It’s also helpful to sweep your ramp before each use, as all it takes is one stray piece of gravel to cause you to go flying
Enjoy your new ramp and take satisfaction in knowing that you built it yourself and will know exactly how to fix it if you encounter any issues.
Thanks for the final photo shoot Steve!
You Might Also Like...
How to Make a 3ft. Mini Ramp
This mini ramp is 3ft. tall (from the ground to the top of the deck), 8ft. wide and 24'-0 from end to end (including each deck).
Aswith all structures here on DIYskate, you can build this mini ramp anysize you want. However, for the material list to be accurate, you willneed to follow the plans as listed below.
Keep in mind thatthis ramps measurements was not chosen at random. I spent weeksengineering a ramp that would be cost and material efficient, fun toride and most important, sturdy and safe.
Where to get your Supplies
The wood and hardware can befound at most home improvement stores. Sometimes you can find the steelthere as well, I know my local Home Depot carries the coping andthreshold material.
If not, check the phone book. Look up Steel, Steel Yards, Steel Fabricators, Scrap Steel & anything else with Steel in the title.
Ifthis ramp is going to stay outside, it needs to be protected from theelements. A good place to start is with pressure treated lumber, paintand a tarp. You may want to invest in a composite material for thesurface too. Such as Skate Lite or Ramp Armor.
Be extra careful when working with treated lumber though, the chemicals used to treat the wood contain a poisonous pesticide.
Choosing a Location for your Mini Ramp
Ideally, alevel driveway or concrete pad would be the best spot for your miniramp. But ramps tend to get pretty big and backyards and fields end upbeing the only place large enough for them.
If you're placingyour mini ramp on terra firma (earth) you'll need to make footings, orpads that the half pipe will sit on. You can do this similar to the wayyou build a deck for a house, with concrete blocks.
I've written a separate page on ramp foundations, because it's more than can be covered in a paragraph.
♠ Ramp Foundations
Build it
Below is a cut list referencing what you will need and it's size.
Material Cut List | ||||||||||||||||||||||||||||||||||||||||||||||||||||||||||||||||||||||||||||||
|
|
|
Transition layout Diagram
Gather two sheets of 3/4' plywood for the side templates. One sheet of 3/4' ply will provide two sides.
Use CDX or better grade plywood. Particle board is not acceptable for any skate structure, period.
Drawing the transition
Take an 8' long 2×4 and on oneend, drill a hole the diameter of a pencil (about 3/8'). Then measurefrom the hole you just drilled, the length of the transition radius. Inthis case, 6'-0. Place a screw there but don't go all the way throughthe 2×4 yet.
Takeyour 3/4' plywood and lay it on a fairly level surface. Grab anothersheet of plywood and place it next to the 3/4' plywood as shown below.
Withthe 2×4 you made earlier, screw the screw into the top piece of plywoodwhere shown above. Now you want to draw a radius using the 2×4 to guideyour pencil until you have the transition radius clearly visible on the3/4' sheet of plywood.
Oncedrawn, measure up 2'-11 1/4 from the bottom left side. Using a straightedge, mark this and the notch for the coping to complete thetransition. The notch for the coping is 1 1/4' by 1 3/4'.
Cut the transition
With a jig saw, very carefully cut on the lines you drew for the transition. Once cut, you can use this as your template to trace the three remaining transition sides.
You'llonly need two 3/4' sides for each 8' ramp section. Most ramps are madein 4' sections but this ramp is small enough to get away with an 8'span. Cut the templates and set them aside.
Framing the Transition
Gather thirty four, 7'-10 1/2long 2×4's for the transition sections. Each 8' wide transition sectionrequires seventeen 2×4's. This includes the deck portion as well.
Takefive of those 7'-10 1/2 long 2×4's and start framing this section byplacing two 2×4's at the back, one at the front and two on the top nextto the coping notch as shown above.
Adding Supports
Place two 2'-9 long 2×4's under the deck 2×4's where shown below. Use about eight, 1 5/8' screws to attach each one.
These add extra support for the deck and need to be placed on each side in both transition sections.
Framing the Transition continued
Now attach twelve7'-10 1/2 long 2×4's, 8' on center unless noted otherwise as shownbelow. Once this has been done, repeat the process for the secondtransition section and set them aside for now.
The2×4's that are doubled in the lower portion of the riding surface arenecessary to create a larger surface area for the seam of the first3/8' plywood layer to.
Framing the Flat Bottom
Gather fifteen 7'-9 long 2×4'sfor the flat bottom supports. You'll also need two, 8' long 2×4's forthe sides of the flat bottom section.
Attach the 7'-9 long 2×4's to the 8' long 2×4's, 8' on center as shown below to finish the flat section.
Pre drill the screw locations at the ends of the 2×4 with a 3/16' drill bit to keep the wood from splitting.
Also, as with the transition, the 2×4's must be doubled where shown for the first layer of 3/8' plywood.
Placing the Ramp
Now that all of the framing is done,the sections can be attached to one another. Hopefully you have theramps final location all squared away too. If not you can learn moreabout ramp foundations here.
Startby having a friend help you move one transition section into place.Then place the flat bottom section next to the transition. Finally,place the last transition section next to the flat bottom section.
Onceall of the sections are in place, make sure that they are level and fittogether properly. Then double check that they are fitting togethercorrectly. After you have done this, clamp the sections together tomake sure they aren't going anywhere. I use quick clamps, but most any clamps will work.
Mini Ramp Plans
Assembling the Ramp
If your mini ramp is on a concreteslab, you can attach the transition and flat bottom sections togetherusing 2 1/2' screws. Screw them together from each side of the bottomwith about six screws per side.
Ifyou are placing your ramp on footings or concrete blocks, drill fourequally spaced 5/8' holes. Now bolt the sections together using four1/2' bolts with nuts and washers per side, as shown below.
Buying the coping
To find the steel, look up 'steel yards', 'structural steel' or 'steel fabricators' and so on in the phone book.
Theactual size of the steel pipe that you are looking for is 2 3/8'(60.33mm) outside diameter. With a wall thickness of 7/32'. This pipeis known by steel shops as...
♠ 2' OD, Schedule 80, black steel pipe
Some steel shops are picky about what it's called so use the above name if they seem confused.
Youcan also use schedule 40 steel pipe (5/32' wall) as it is cheaper andlighter, but it may become dented. Schedule 80 pipe on the other handwill not dent under normal skateboarding use.
Do not use PVC pipe (plastic) or electrical conduit, if you want it to last.
Cutting and Drilling the Coping
Cut your steel pipe into two pieces at 8' long with a steel cutting blade (carbide blade) and miter saw or circular saw.
Now we need to attach the steel coping to the ramp. I am going to cover two of the most common methods.
Thefirst method being screws. If done properly, screws will hold thecoping secure for the life of your ramp. Also, you will rarely if evernotice the holes while skating the ramp.
Start by marking thepipe about 3' in from the ends and then about every two feet inbetween. Now drill a 3/8' on the outside and a 3/16' hole on the insideof the pipe.
Attach the Coping w/ Screws
Once drilled, place thecoping in the notch on the mini ramp. Rotate the pipe so that thescrews will hit the 2×4 close to the center. Now place the screws inthe holes and screw the pipe down snug.
After you're done, go back with a screwdriver and make sure the screws are screwed down tight.
Attach the Coping w/ Bolts
Toattach the coping to the mini ramp with bolts, you will need to drillholes in the 2×4 behind where the coping will sit. Mark the 2×4 aboutan 1 1/2' down from the top, 6' in from each end. Also mark two in themiddle at 2'-4 apart. Drill a 3/8' hole in each marked location at aslight downward angle.
Oncethe 2×4 has been drilled, place the coping in the notch on the miniramp. Use the previously drilled holes to mark the coping. Remove thecoping and drill the 3/8' holes where you have just indicated.
Feed a hook bolt into the holes youdrilled and place the coping in the notch on the mini ramp, whilelining up the bolts with the holes in the 2×4. Tighten the bolts downsecure to the 2×4 using nuts and washers.
The bolt at the bottom of theillustration on the right is also known as a clothesline hook and isthe most common for this application. However, hook bolts come in avariety a shapes and sizes. You can use almost any of them as long asthey are about 3' in length and have a 3/8' diameter.
Covering the Decks
Now that you have the coping all taken care of, it's time to cover your ramp. Start with the decks.
Cuttwo sheets of 3/4' plywood down to 2'-9 wide. Attach a sheet to eachdeck portion of the ramp with 1 5/8' screws. Space the screws about afoot apart from each other on the studs below.
Youmust hit the 2×4 supports with the screws. A good way to accomplishthis is with a chalkline or straight edge and pencil. Use the screws onthe sides of the ramp as guides for the 2×4 supports.
Covering the Ramp
Place a sheet of 3/8' plywood on theramp. Push it flush against the coping and begin attaching the ply with1 5/8' screws. Start at the top and work your way down, going from leftto right like reading a book. You may need someone to help you hold theply in place while you get the first few screws started.
As with the deck, mark the location of the 2×4 supports and space the screws about a foot apart.
Next,take another sheet of 3/8' plywood, push it flush against the previoussheet and attach it in the same way placing the screws about a footapart.
Once you've attached the first two pieces, do the same to the other side of the ramp leaving the center exposed as shown above.
Theidea is, you shouldn't have to cut the center sheet for it to fit. Thespace should work out to four feet. But if you do have to cut thesheet, it's much easier to figure it out here than on the transition.
Second Layer of Plywood
On the second layer, you don'twant the plywood seams to be in the same place as the bottom layer. Socut a sheet of 3/8' plywood in half and attach it to the ramp the sameway as the others.
Keep adding full sheets until you reach the other side and the coping. Cut the last ply to fit if necessary.
Attaching the Final Layer
Start with a full sheet ofmasonite and press it flush against the coping just like the firstlayer. Keep adding sheets until you reach the other side. Once again,cut the last one to fit if necessary.
The coping should stick out 3/8' fromriding surface. If it sticks out too much, place wood shims under themasonite, near the coping to raise the masonite. Shims are available atyour local hardware store.
Mini Ramp Radius
Themain difference with masonite is that you need to countersink the screwhole locations before you screw the masonite down. You can do this witha countersink bit, or a 3/8' drill bit and a steady hand.
You also will need to space the masonite sheetsabout 1/16' to 1/8' from each other. This keeps them from bubbling upwhen they expand due to temperature change. I use pennies to space them.
Free Mini Ramp Plans
Finished 3ft Mini Ramp
Check everything before you skate it, but you are done. I didn't add a railing because the ramp is only 3'.
If you have made it this far, you are the proud owner of a brand new 3' mini ramp.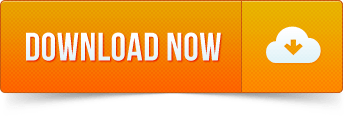